Autopilots at Mercedes-Benz: “Automated driving” – a new proving method for state-of-the-art safety systems
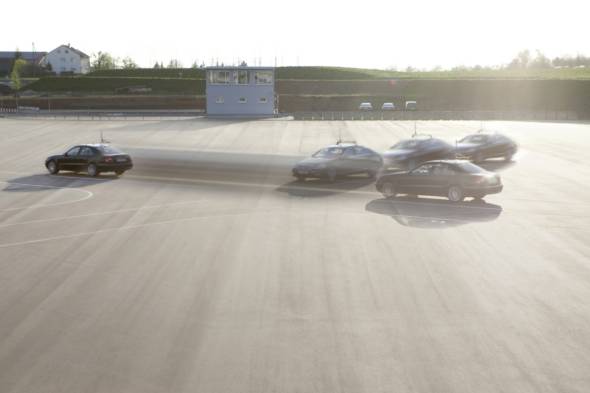
With an eye on future generations of driver assistance systems, Mercedes-Benz is the first vehicle maker worldwide to introduce an innovative proving method into its test driving portfolio – safety-critical driving manoeuvres that cannot be precisely reproduced by human drivers are now being handled by autopilot on closed test tracks. “Automated driving” supports the development, testing and validation of assistance systems and other vehicle safety features. Testing at the limit can now be carried out without danger and health risks to development engineers, delivering clear benefits to Mercedes-Benz customers – because the tests are carried out with the highest degree of precision, future assistance systems can be developed and validated to Mercedes-Benz’s exacting quality standards despite increasing levels of complexity.
For years, Mercedes-Benz has been setting benchmarks in the development of new technologies for the continuous improvement of active and passive safety in automobiles. Innovations in passive safety such as the rigid-form passenger cell, crumple zone, airbag and three-point safety belt, plus active safety like ABS, ESP® and brake assist all trace back to Mercedes-Benz. They have made a substantial contribution to improving traffic safety and to reducing significantly the number of injuries and deaths among road users.
The current status of active safety technology is defined by intelligent assistance systems that turn the vehicle into a “thinking partner” – one that can see and feel, and that can react in the event of danger. Systems like the blind spot assistant, ATTENTION ASSIST and the night view assistant are focused specifically on accident problem areas such as lane changes, fatigue or poor visibility at night.
“With future driver assistance systems, we will be able to address even more complex traffic situations and therefore to ease the dangers of further accident hot spots – like intersections,” says Prof. Bharat Balasubramanian, Head of Product Innovations & Process Technologies at Corporate Research and Advanced Engineering Daimler AG. “Our new automated driving test methods help us to fulfil the extremely high quality and operational safety demands placed on our safety systems more efficiently.”
Autopilots ensure greater precision and relieve development engineers
In addition to established methods, Mercedes-Benz will fulfil requirements for reliable functionality and operational safety in future assistance systems through the “automated driving” of test manoeuvres on dedicated proving grounds. Prototypes used for this purpose are usually series production vehicles equipped with “robots” for steering, acceleration and braking. An on-board computer controls the autopilot so that a pre-programmed course is followed exactly – even if several vehicles are involved in one manoeuvre.
Test engineers in the control centre monitor all events and can stop the vehicles at any time. In parallel, the vehicles perform self checks and brake automatically if they register deviations. Thus, the test configuration is safe, yet flexible. All Mercedes-Benz models can be equipped with the technical equipment for “automated driving”. Moreover, a large variety of different safety systems and equipment can be tested.
Using “automated driving”, engineers analyse safety innovations under real-life conditions in the vehicle, addressing two critical challenges:
- Reproducibility. In order to calibrate the systems under test exactly, extensive variations and repetitions of tests are needed. In so doing, all parameters such as vehicle distances, speeds and steering angles have to meet specifications and always need to be maintained precisely in order to guarantee comparability.
- Safety. Because the systems are intended to kick in only in critical situations, such scenarios must be induced during testing. The manoeuvres demand precision timing and should not create a real danger for anybody.
Both requirements are usually beyond human abilities – humans cannot react quickly enough and cannot repeat manoeuvres with the desired accuracy. However, for complex in-vehicle electronic systems and for assistance systems in particular, such driving tests are indispensible as their functional validation must be carried out in a manner that is comprehensive and as close to reality as possible.
The repeat accuracy of the test methodology enables test vehicles to maintain a pre-determined speed and course exactly and to brake very precisely. For example, if a vehicle drives a pre-planned course several times, the tracks of all the runs vary from one another by less than two centimetres. Should the vehicle be brought to a complete halt at a particular location, the end points of all braking manoeuvres are within a radius of three centimetres.
Alongside the proving of assistance systems, “automated driving” will also be used for so-called “extreme tests” in future. These put the vehicle under loads that are well in excess of those reached under normal use in traffic. The intention is to ensure, for instance, that airbags are not activated unintentionally should the car be driven heavily over a ramp or against a kerb. Test drives that involve a high degree of physical stress for the driver can thus be avoided.
State-of-the-art test methods for the highest safety demands
In their development work, Mercedes-Benz engineers use the results from the company’s in-house accident research, which delivers important findings. Several combined validation methods guarantee that all systems function reliably at any critical moment. Company philosophy insists on validation to go considerably farther than required by regulatory standards. When it comes to passive safety, Mercedes-Benz internal crash test requirements go well beyond meeting public crash test standards.
The combination of computer simulations and real-life crash tests ensures passive safety to Mercedes-Benz standards. Mercedes-Benz also makes use of state-of-the-art, networked test methods when it comes to active safety. Drive simulator tests combined with simulation procedures deliver a faster and more reliable development process and complement test drives under real-life conditions. “In Sindelfingen, we are currently building a new driving simulator. The state-of-the-art technology of this equipment will make the future development of new safety systems even faster and more precise,” confirms Balasubramanian.
Automated driving as the basis of future innovations
Mercedes-Benz is the only vehicle maker in the world to use “automated driving” as an additional element in the testing process. It will be used on dedicated proving grounds in tests that would be virtually impossible to reproduce manually, like merging at different speeds and vehicle distances; high-risk tests where, for example, a vehicle brakes heavily in front of another that swerves at the last minute; and safety-critical tests where, at an intersection, one vehicle crosses just in front of or behind the path of a second vehicle.
With “automated driving”, Mercedes-Benz has developed a new, unique testing method for safety systems. It is yet further proof of the innovative power of Mercedes-Benz. The new test method guarantees the fast and efficient development of assistance systems to the highest levels of quality and reliability and also offers maximum safety at work for employees.
Bharat Balasubramanian sums up: “In order to continue to set trends in the field of safety in future, our test procedures must be able to keep pace with the wealth of ideas generated by our engineers. With automated driving, we feel we are well equipped for the development of the next generation of assistance systems.